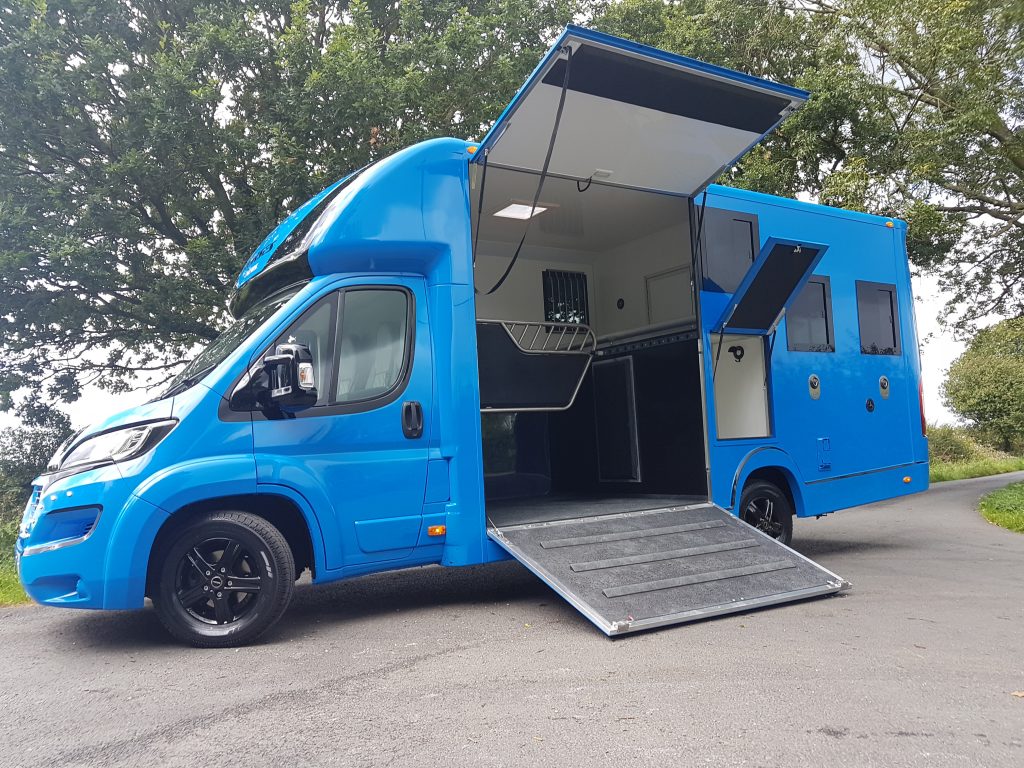
Horsebox Flooring a VBRA Best Practice Guide
Horsebox flooring has been is an area of concern for both Horsebox manufacturers, converters, horse transport companies and horse owners who have their own lorry or trailer. We have put together some solutions as a best practice guide.
Problems seem to stem from either lack of experience when fitting floors, cutting corners to save money at the new build, or conversion stage from a box, parcel van, panel van or when refitting flooring, also from lack of inspection and maintenance.
Underframe.
We will start with the conversion (e.g. from parcel van) and below the floor, as many of this type of vehicle has wider bearer spacing than horse box bodies as much as 24”/ 600mm and perhaps even greater over the rear wheels. Horses have a large mass on a small hoof area and have a habit of lifting a foot whilst standing. This coupled with a phenolic floor (Buffalo board Wisadeck etc) of perhaps 18mm or Keruing 22mm planks is not always adequate for horse box application. The floor may require removal and fitment of additional reinforcing bearers, drain holes or drain channels and sealing all floor joints, cut edges and screws is one solution and is often beneficial on payload compared to double flooring.

Notes.
The bearer spacing determines the floor thickness so if the body is a conversion then the board supplier will spec the floor to the spacing already in situ. A manufacturer of new builds may space bearers at from 400 to 600 mm dependant on the size of horse to be carried with perhaps a closing up of the spacing in the vicinity of where the hooves will be when travelling and the board manufacturer should advise on the floor based on the spacing.
With “Rumber” the manufacturer specs the spacing at 300mm and there would no alteration from this as the flooring only comes in 1 thickness. This spacing must be adhered to.
Floor Overlay
Another route is an additional overlay of flooring which is often cheaper if you can afford the payload loss. Using Aluminium Five bar tread plate in either 3 or 4mm or another layer of Phenolic faced plywood or as a last resort marine ply certified to BS1008 and sealed on the face and underneath with a waterproof coating and in all instances incorporating drain tubes or channels, with all screws, joints and cut edges sealed. The floor rubber mats can then be refitted on top.
Fitting new flooring
The use of marine ply which is a poor substitute to the other flooring options and should be avoided, extra care must be taken on sealing not just edges, but both upper and lower faces of the board. Failure to install, seal and carefully maintain a marine ply flooring can result failure in less than eighteen months.
Next, Phenolic faced ply. These boards come with cores of either far eastern hardwood or Birch. The Birch cored boards are the strongest, although both are made for hard use, choose wisely as there are different thicknesses and patterns of top resin veneer. The board manufacturer or supplier should be able to spec their best board for horse box use based on your bearer spacing. Problems arise from any cut edges and screw holes. Use the recommended sealer by the board manufacturer.
Some manufacturers recommend an acrylic type sealing paint/compound which is applied 3 times and allowed to dry each time to all cut edges) or a suitable alternative
(e.g. Smith’s CPES epoxy sealer) combined with a One-part Polyurethane sealant/adhesive
(e.g. Sikaflex) between the sheets and down the screw holes. It can help to fit flange head screws to phenol flooring that will not crack the resin surface of the board as the screw tightens on the surface like a countersunk screw would. Its best to cover the area over the wheels with a thin sheet of GRP or Aluminium to help protect the flooring from the rain/dirt thrown up from the wheels before the fitting of timber-based flooring.
Keruing hardwood flooring is quite strong compared with phenol flooring and weighs only slightly more on the same thickness. It still needs to be dried out regularly to avoid rot and the only other issue is that horses lifting a leg can load just 1 board so for long term is best overlaid with phenol boards or aluminium sheet sealed as in the next paragraph.
When fitting Aluminium planks or sheets seal between all planks, sheet joints, cuts and holes with PU sealing compound. Drain tubes or preferably drain channels should always be fitted unless the construction deems them unnecessary. Aluminium flooring is not impervious to corrosion and any areas that have hollowed over time or gaps between overlays of matting can become filled with dirt straw etc which works its way between the sheets and holds onto horse urine greatly increasing the reaction between the urine and the aluminium. Note! To avoid Galvanic corrosion between the flooring (Aluminium) and dissimilar metal bearers (Steel), always use a gasket to prevent this corrosion.
e.g. Rubber, Fibre, Gaffer tape, PU Sealer or CT1 grab & bond, the same precautions must be remembered when riveting, do not use Aluminium rivets on stainless steel.
There is another type of flooring called Rumber which is a tongue and groove plank made from old tyres with some plastic binder added. This flooring would have to be imported as at present there are no UK stockists. The bearers need spacing at 305mm centres and the flooring is the same weight as 27mm phenol board and 12mm rubber matting around
38kg sq. mtr. It will not rot and needs no further protection is non-slip and has a lifespan of around 20 years. With the additional floor supports it would add around 2kg per sq. mtr to the payload.
Floor overlay and maintenance
Floor overlays come either as lift out rubber mats or flow coated rubber type compounds. Each type has its downsides.
Loose rubber mats need to be taken out preferably after each use for best practice, and in any case at least 3 or 4 times per annum to allow the floor to dry. The floor washed out and all sealant around edges and drain tubes should be checked periodically.
Sealed flow-coat flooring needs to be washed out to inspect and should be done again on a regular basis also check the condition of the flow-coat for cracking/wear, as water, urine and chemicals under the coating will rot the floor in a very short time.
Inspection of the floor should be not only on the top but also on the underside for cracking rot etc including under the wheel arches.
Aluminium sheets/ planks are also affected from both urine, chemicals and cracking especially where there are large bearer spacings so don’t forget to inspect these.
How often is dependent on use but could be incorporated in the drivers walk around check if only used occasionally. It is cheaper to spend half an hour checking the soundness of a washed dry floor before using your horsebox than have the trauma of an injured horse.
Panel Van Conversions,
With this type of flooring laid on the panel van metal floor it cannot be checked from below. It is imperative that it has regular inspection of the sealing and of any cracking or wear in the floor. Some of this type of horse transport have flow-coat floors over relatively thin phenolic or marine ply, wonderful and robust until you have damaged the coating or have failing sealant. If you have had damaged flooring that has not been attended to quickly and does not look sound, the only option is to lift out the floor and inspect underneath. And whilst the top floor is out the metal van floor can be checked as the top floors are not always drained with properly sealed tubes so that liquid between the floors cause corrosion and rot.
Inspection Notice
It is good policy to put a notice in the cab/living or the horse bay entrance, on how to check and maintain the floor.
Remember the safety of occupants and animals should always be a priority. The horse can suffer trauma if it goes through a floor even if physically uninjured it could still be psychological giving future problems with both loading and travelling.
EXAMPLE:
- After every Use of this horsebox, Remove rubber matting (if applicable)
- Wash out floor and allow to dry!
- When Dry check seals around edges, drain tubes etc, and any worn areas of floor covering.
- Feel for any unusual softness/springiness in any areas as you walk over the floor.
- Check under the floor for rot, cracks, missing underseal if applied especially over large bearer spacings.
Your first priority is the safety and welfare of your horses.
This guide is for the benefit of all Horsebox owners and users and all VBRA members are expected to adhere to this guidance